To optimize the particle packing of the castable, different types of aluminum oxide micropowders can be used to form the matrix. These include calcined, semi-reactive, unimodal, or multimodal alumina micropowders. Effect of specific particle size distribution (PSD) of various alumina micropowders on low cement castable properties. And compare the addition of different types of water-reducing agents to understand their impact on the finished castables.
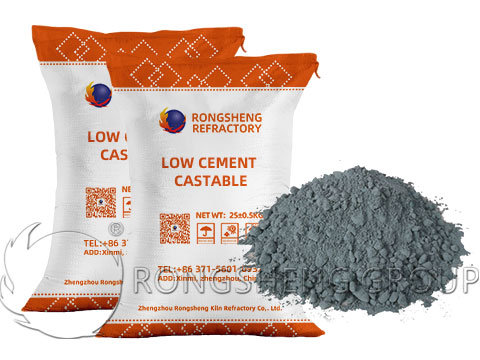
Selection of Aluminum Oxide Powder
The alumina micropowders used in the test include calcined alumina micropowder, bimodal activated alumina micropowder, and single-modal activated alumina micropowder. The test was conducted using low-cement castables with tabular corundum as aggregate, and the castable formula was optimized using the particle gradation models of DINGE and FUNK. The constant coefficient is set to 0.27. The first series studies the application of 3um calcined alumina products, which are divided into castables without silica fume and castables containing silica fume. In the second series, 3um calcined alumina and different proportions of unimodal activated alumina are added as the matrix to achieve bimodal alumina performance. The final series examines the effect of bimodal alumina on the particle size distribution in low-cement castables. When the amount of water added in each series is constant, the construction performance, fluidity, cold flexural strength, and load softening temperature of the castables are measured.
The Influence of Aluminum Oxide Powder on Castables
Research shows that not only the d50 of alumina micro-powder but also its particle size distribution curve is crucial to optimizing the rheological properties of alumina-based low-cement castables. By adjusting the shape of its particle size curve, the possibility of using 3um calcined alumina to have suitable flowability in many castables increases. In applications that require lower water additions, the calcined product can be compounded with single-modal active oxidation micron powder to achieve the desired particle filling optimization. For bimodal alumina, controlling the particle size distribution, with the presence of very fine particles in d10 and good top cut in d90, can increase flowability, reduce mixing time, and improve physical properties. In addition to the particle size distribution of alumina, additives play an important role. There are differences from one alumina to another, and additives should be selected and adjusted according to the type of alumina.
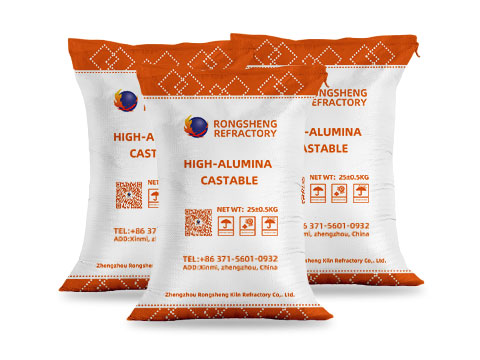
60 Refractory Castable GL60 High Aluminum Refractory Castable Boiler Hot Blast Stove Refractory Castable
Refractory castables made of high-aluminum raw materials as aggregates and powders, and adding binders. It has high mechanical strength and good thermal shock resistance and abrasion resistance. It is mainly used as the lining of boilers, blast furnaces, heating furnaces, ceramic kilns, and other kilns.
GL60 high-aluminum refractory castable is synthesized from high-aluminum refractory aggregates, powders, binders, and admixtures in proportions. It has the characteristics of good high-temperature performance, high durability, wide operating temperature, and no shrinkage or damage. It is widely used in hardware, smelting, chemical industry, non-ferrous metals, and other industries, especially in the steel industry. Mainly used in rotary kiln front kiln mouth, dismantling furnace, kiln head cover, and other parts. High aluminum castables are divided into conventional and low steel types and steel types.
60 refractory castable, boiler hot blast stove refractory castable, is a refractory castable made of high alumina bauxite clinker as aggregate and powder, adding binder and dispersant. The integral lining material can be poured directly or refractory prefabricated parts can be spliced together.
RS refractory material manufacturer has an environmentally friendly, fully automatic unshaped refractory material production line. Our refractory products have been sold to more than 100 countries around the world. The product quality is reliable, and the formula of refractory materials can be customized according to the customer’s actual working conditions. For product packaging, we use 25kg/bag or 50kg/bag woven bags according to user needs and then use ton bags. Contact us for a free refractory lining solution and quote.