Refractory cement is a type of special cement. It has very high-temperature resistance and is usually used in buildings, industrial equipment, and furnaces in high-temperature environments. The main components of refractory cement are clinker, silicate, aluminate, and other substances. The special combination of these substances gives refractory cement excellent fire-resistant properties.
Refractory Cement Product Introduction
Refractory cement has a wide range of applications. It can be used in various fields such as construction, metallurgy, the chemical industry, and electric power. In the field of construction, refractory cement is mainly used in buildings in high-temperature environments, such as blast furnaces, electric furnaces, steel plants, aluminum plants, etc. In the metallurgical field, refractory cement is mainly used to manufacture high-temperature furnaces and refractory materials. In the chemical industry, refractory cement is mainly used to manufacture chemical equipment and storage tanks. In the electric power field, refractory cement is mainly used to manufacture chimneys, boilers, and burners.
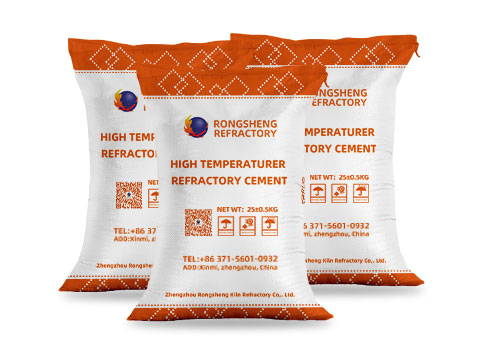
Characteristics of Refractory Cement
- Good high-temperature resistance. The main feature of refractory cement is its ability to maintain stable performance in high-temperature environments. Usually able to withstand high temperatures up to 1500°C.
- Good chemical corrosion resistance. Because refractory cement contains a large amount of chemical components such as alumina and silica. Therefore, it can resist the erosion of strong corrosive substances such as acids and alkalis.
- High compressive strength. Refractory cement has high compressive strength and can withstand large amounts of pressure. Therefore, it is widely used in construction, metallurgy, and other industries.
- Refractory cement has strong plasticity. Refractory cement has better processing performance. Refractory products of various shapes and sizes can be made through different processing techniques.
The production process of refractory cement is very complex and requires the use of high-tech technology and advanced equipment. The production process requires strict screening and proportioning of raw materials to ensure the physical and chemical properties of refractory cement. The production process also requires high-temperature calcination and fine processing to ensure the quality and stability of refractory cement.
What are the Precautions for Using Refractory Cement?
- Refractory cement and refractory clay are both types of refractory materials. The refractory degree of refractory cement is 1500 degrees Celsius. It has high strength after solidification, and the grade can reach 625. It is mainly mixed with bauxite aggregate to form refractory concrete with high refractory resistance. The refractory clay has a refractory resistance of 1000°C, has no strength after solidification, and only plays a certain bonding role. Refractory clay is usually used to build refractory bricks or to paste furnace walls.
- If refractory cement and refractory soil are mixed and used, the use value of refractory cement will be greatly reduced. This is equivalent to mixing refractory cement and loess and using them together. The solidification strength and grade of refractory cement will be greatly reduced, the material will easily fall off, has no strength, and has a short service life. It is recommended that workers engaged in furnace construction strictly mix refractory cement and refractory soil during the construction of refractory materials.
What are the precautions for using refractory cement? Familiar with the characteristics of refractory cement and the requirements of the use environment. If you strictly follow the construction instructions, you will be able to maximize its advantages.